Concrete Floor Grinding Cost Per Square Foot
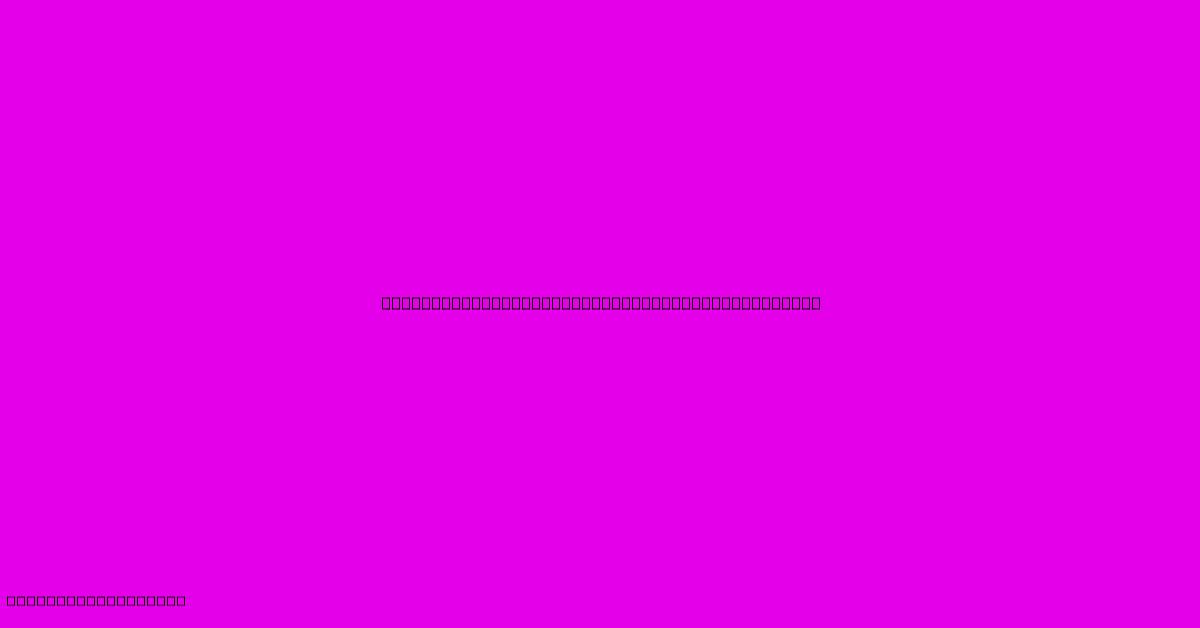
Discover more detailed and exciting information on our website. Click the link below to start your adventure: Visit Best Website meltwatermedia.ca. Don't miss out!
Table of Contents
Unveiling the Concrete Floor Grinding Cost: A Square-Foot Breakdown
Hook: What determines the true cost of grinding a concrete floor? Understanding the variables impacting this expense is crucial for successful project budgeting and execution.
Editor's Note: This comprehensive guide to concrete floor grinding cost per square foot was published today.
Why Important & Summary: Concrete floor grinding offers significant aesthetic and functional improvements, transforming dull, damaged concrete into smooth, polished surfaces. This guide breaks down the cost factors – equipment, labor, material, and project specifics – providing a clearer understanding of what influences the final price per square foot. This analysis includes considerations for different grinding levels, surface preparation, and potential add-ons, offering a realistic cost projection for various projects.
Analysis: This guide is based on extensive research encompassing industry pricing data, contractor quotes, and material cost analyses. The information synthesizes multiple data points to provide a reliable cost estimate range, acknowledging that specific project costs can vary significantly.
Key Points:
a. Cost varies widely depending on several factors. b. Accurate estimation requires a site-specific assessment. c. Understanding the process enhances cost control.
Concrete Floor Grinding: A Comprehensive Cost Analysis
Introduction: Concrete floor grinding offers a versatile and durable solution for various applications, from industrial facilities to residential spaces. Understanding the cost involved is paramount to successful project planning. This section analyzes the key cost components contributing to the price per square foot.
Key Aspects:
- Grinding Level: The desired level of grinding significantly impacts cost. Simple surface leveling may cost less than achieving a highly polished finish.
- Square Footage: The overall size of the area to be ground directly influences the total cost. Larger areas typically benefit from economies of scale.
- Surface Condition: Pre-existing damage, like cracks, stains, or significant imperfections, requires extra preparation, increasing cost.
- Location: Geographical location affects labor rates and material costs.
- Contractor Experience and Expertise: Experienced contractors may charge higher rates but offer greater efficiency and quality.
- Materials: The type of grinding equipment, diamond tooling, and any required sealers or coatings affect costs.
Discussion: Each aspect plays a vital role in determining the final cost. Let's explore each in greater detail.
Grinding Level: From Leveling to High Polish
Introduction: The desired level of grinding directly correlates to the time and effort invested, hence impacting the cost.
Facets:
- Leveling: Removing surface irregularities and creating a flat, even surface. This is the least expensive option.
- Honing: Refining the surface for a smoother finish. Requires more time and specialized tooling.
- Polishing: Achieving a high-gloss, reflective finish. Demands the most time and the use of progressively finer diamond tooling.
Summary: The choice of grinding level dramatically influences the cost per square foot. While leveling offers a budget-friendly solution, polishing significantly increases expenses.
Square Footage: Economies of Scale
Introduction: The size of the area impacts the overall project duration, labor hours, and material consumption, thereby influencing cost-effectiveness.
Further Analysis: Larger projects often benefit from lower per-square-foot costs due to the efficiencies of working on a larger scale. However, it's crucial to factor in potential equipment adjustments or additional labor requirements for extensive areas.
Closing: While larger projects might seem initially more expensive, they usually yield lower per-square-foot rates due to economies of scale.
Surface Condition: Pre-Existing Damage
Introduction: The initial condition of the concrete floor significantly impacts the preparation work required, thereby influencing the overall cost.
Further Analysis: Severe damage such as deep cracks, large holes, or extensive staining necessitates extra time and materials for repair and preparation before grinding can begin. These repairs add to the overall cost per square foot.
Closing: A thorough assessment of the existing surface condition is crucial for accurate cost estimation, especially considering the potential for unforeseen repair needs.
Location: Geographic Variations
Introduction: Regional differences in labor rates, material costs, and local regulations impact the final price.
Further Analysis: Metropolitan areas typically have higher labor and material costs compared to rural regions. Transportation costs for materials and equipment can also increase expenses in remote locations.
Closing: Considering location-specific factors is essential for realistic cost projections, accounting for variations in regional pricing.
Contractor Selection: Experience and Expertise
Introduction: Choosing a qualified contractor influences both cost and project quality.
Further Analysis: Experienced contractors possess the necessary skills, equipment, and knowledge to deliver efficient, high-quality results. While their rates may be higher, their efficiency can often offset the additional cost in the long run.
Closing: Thorough research and due diligence in selecting a reputable and experienced contractor are vital for project success and cost control.
Material Costs: Equipment, Tooling, and Sealers
Introduction: The cost of diamond tooling, grinding equipment, and any required sealers or coatings significantly contributes to the overall expenses.
Further Analysis: Diamond tooling comes in various grits, each suitable for specific grinding stages. Higher-quality tooling may cost more initially but may offer superior performance and durability, potentially offsetting costs over time.
Closing: The choice of materials directly impacts the cost, necessitating careful consideration of quality, durability, and long-term value.
FAQ
Introduction: This section addresses frequently asked questions about concrete floor grinding costs.
Questions:
- Q: What is the average cost range for concrete floor grinding per square foot? A: The cost typically ranges from $2 to $10 per square foot, depending on the factors discussed above.
- Q: What factors most heavily influence the final cost? A: Grinding level, square footage, surface condition, and contractor expertise are major cost drivers.
- Q: Are there ways to reduce the cost of concrete floor grinding? A: Careful planning, choosing a less intensive grinding level, and selecting a contractor with competitive rates can help manage expenses.
- Q: What is included in the cost of concrete floor grinding? A: The cost generally includes labor, equipment rental or purchase, diamond tooling, and potentially site preparation and cleanup.
- Q: How long does a concrete floor grinding project usually take? A: Project duration depends on the size of the area, grinding level, and surface condition, ranging from a few hours to several days.
- Q: Is it necessary to seal a concrete floor after grinding? A: Sealing is recommended to protect the polished concrete surface from stains and damage, extending its lifespan and maintaining its aesthetic appeal.
Summary: Understanding these FAQs enhances project planning and enables informed decisions.
Tips for Managing Concrete Floor Grinding Costs
Introduction: Effective cost management strategies can significantly influence the final price.
Tips:
- Obtain Multiple Quotes: Compare estimates from different contractors to identify competitive rates.
- Thoroughly Assess the Surface: Identify any pre-existing damage to factor it into the cost estimate accurately.
- Choose the Right Grinding Level: Select the appropriate grinding level based on your needs and budget.
- Consider DIY vs. Professional: Weigh the pros and cons of attempting DIY grinding against hiring a professional.
- Negotiate Prices: Discuss potential cost savings with contractors, particularly for larger projects.
- Plan for Contingencies: Include a buffer in your budget to accommodate potential unforeseen issues.
- Explore Financing Options: Inquire about financing options if the project cost exceeds your current budget.
Summary: Proactive cost management strategies ensure efficient spending and successful project completion.
Summary: Concrete Floor Grinding Cost per Square Foot
Summary: The cost of concrete floor grinding varies significantly based on the project’s specifics. Factors like grinding level, surface condition, square footage, contractor selection, and location all play vital roles. Careful planning, thorough assessment, and a strategic approach are key to managing costs effectively.
Closing Message: Investing in a professionally ground concrete floor enhances both aesthetics and functionality, transforming spaces while offering long-term durability. By understanding the cost factors, you can make informed decisions to achieve a cost-effective and successful project.
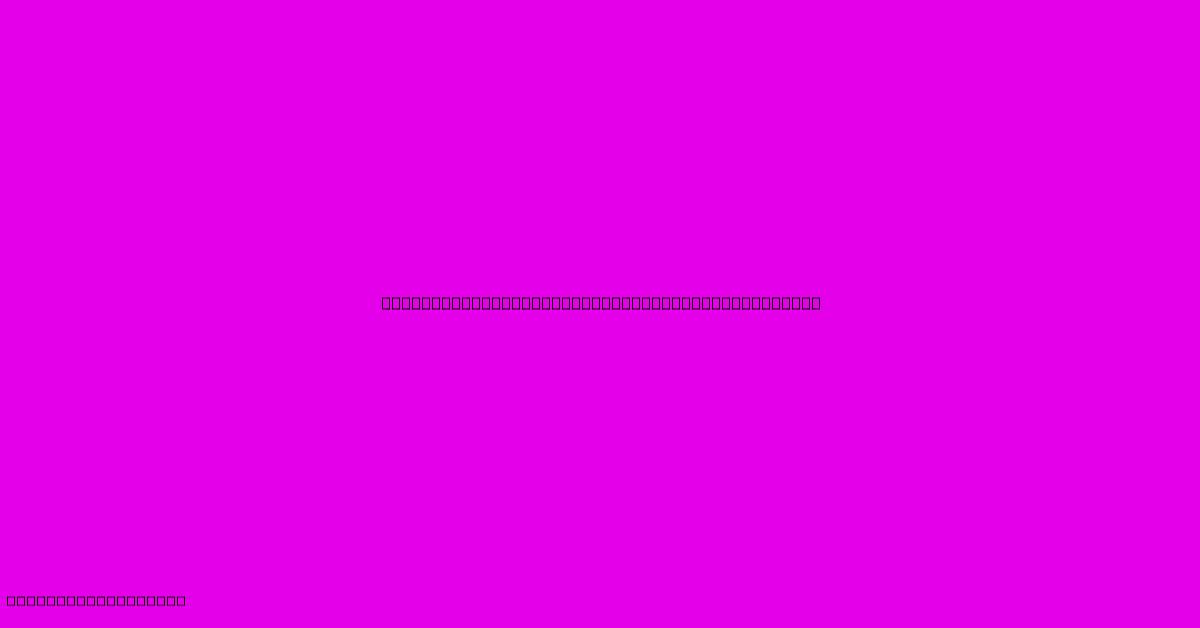
Thank you for visiting our website wich cover about Concrete Floor Grinding Cost Per Square Foot. We hope the information provided has been useful to you. Feel free to contact us if you have any questions or need further assistance. See you next time and dont miss to bookmark.
Featured Posts
-
Blood Is On The Dance Floor
Jan 08, 2025
-
Best Mattress For Floor Sleeping
Jan 08, 2025
-
Carpet Flooring Los Angeles
Jan 08, 2025
-
Best Way To Cut Peel And Stick Floor Tiles
Jan 08, 2025
-
Cat Sleeping On Floor
Jan 08, 2025